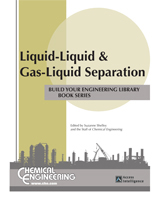
CHAPTERS: Chapter 1. Distillation; Chapter 2. Absorption and adsorption; Chapter 3. Crystallization; Chapter 4. Evaporation and condensation); Chapter 5. Vacuum processing; Chapter 6. Data and calculations; Chapter 7. Related topics
CHAPTER 1. DISTILLATION
Designing azeotropic distillation columns
Stanislaw Wasylkiewicz and Leo Kobylka, AEA Technology Engineering Software, Hyprotech Ltd., Marco Satyro, SEA, Inc.
Extractive distillation: Separating close-boiling-point components
Fu-Ming Lee, GTC Technology Corp.
Recovering and recycling low-boiling alcohols and ketones
George Schlowsky and Brian Loftus, Koch Modular Process Systems LLC
Partitioned distillation columns Why, when and how
Hans Beckeer, Sven Godorr and Helmut Kreis, Linde AG; James Vaughn, Sasol Technology
Separation using coupled reactive distillation columns
Erik Stein, Achim Kienle, Kai Sundmacher, Max-Planck-Institute for Dynamics of Complex Technical Systems
Advanced distillation saves energy and capital
Frigyes Lestak and Cyril Collins, M.W. Kellogg Ltd.
Catalytic distillation extends its reach
Kerry Rock, Gary Gildert and Tim McGuirk, CDTech
Distillation tower flooding More complex than you think
Simon Xu and Lowell Pless, Tru-Tec Services, Inc.
Giving insight to difficult distillations by replotting the McCabe-Thiele Diagram
James Ryan, Ryan Consulting
Distillation reboiler startup can pose challenges
Etienne Rubbers, Kirsten Green and Terry Fowler, Sasol Technology Pty Ltd., and Hendry Kister and Walter Stupin, Fluor
Solving a tower’s salt-plugging problem
Henry Kister, Fluor Daniel , Shihan Chen, Honeywell International
CHAPTER 2. ABSORPTION AND ADSORPTION
Simplify calculations for absorption with chemical reactions
Jerry Meldon, Tufts University
Selecting the solvent for SO2-removal absorption
Soumitro Nagpl and P.K. Sen, Engineers India Ltd.
Scrubbers with a level head
George C. Pedersen, Kimre, Inc ., and P.K. Bhattachararjee, U.S. Agri-Chemical Corp.
Wet scrubbers: Choose the best chemical reagent
Ing. Noe Ugo Rinaldi, Tecnochim s.r.l
Wet scrubbers: Match the spray nozzle to the operation
Lothar Bendig, Lechler GmbH & Co. KG
Taking stock of activated carbon’s many talents
Stephanie Carr and Robert Vaughn, Calgon Carbon Corp.
Removing H2S from gas streams
Gary Nagl, U.S. Filter Gas Technology Products
Prevent thermal runaways in carbon beds
Thomas Hofelich, Marabeth LaBarge, and Denise Drott, Dow Chemical Co.
CHAPTER 3. CRYSTALLIZATION
Simplify multicomponent crystallization
Joseph Schroer, University of Massachusetts (Amherst) and Ka M. Ng, Hong Kong University of Science and Technology
Making big crystals
Richard C. Bennett, Crystallization Technology, Inc.
Crystallization’s forgotten facet
Wayne J. Genck, Genck International
Coping with crystallization problems
B.C. Sutradhar, Invista, Inc.
Better growth in batch crystallizers
Wayne J. Genck, Genck International
CHAPTER 4. EVAPORATION AND CONDENSATION
Optimizing process vacuum condensers
James R. Lines and David W. Tice, Graham Manufacturing Co.
Gravity effects in horizontal condensers
Alejandro Anaya Durand, Cynthia A. Aguilar Guerrero, Edgar Amaro Ronces, National Autonomous University of Mexico
A shortcut for designing evaporators
Alejandro Anaya Durand, Instituo Mexicano del Petroleo
Scaleup of agitated thin-film evaporators
William B. Glover, LCI Corp.
CHAPTER 5. VACUUM PROCESSING
Improving vacuum systems
Terrence Fay and Jarema N. Kraus, Lockwood Greene Engineers, Inc., Mitchell J. Levy, Consultant
Difficult to process? Vacuum it!
Andrew J. Eckles, Atlanta Technology Group
Proper piping for vacuum systems
Loren Wetzel, Graham Manufacturing Co.
Choose the right vacuum pump
Joe Aliasso, Graham Manufacturing Co.
CHAPTER 6. DATA AND CALCULATIONS
Simplify flash calculations
Philip Eubank, M. Sam Mannan and Kenneth Hall, Texas A&M University
Use a spreadsheet to fit vapor-liquid equilibrium data
Victoria Paulsen, Koch Modular Process Systems LLC
Solubility & Henry’s Law constants for sulfur compounds in water
Carl Yaws, Praveen Bajaj, and Harman Singh, Lamar University, Ralph Pike, Louisiana State University
Solubility and Henry’s Law constants for amines in water
Carl Yaws, Jack Hopper and Sunil Mishra, Lamar University
CHAPTER 7. RELATED TOPICS
Apply liquid-liquid extraction to today’s problems
Roger W. Cusack and Donald J. Glatz, Glitsch Process Systems, Inc.
Difficult liquid-liquid separations
Thomal H. Wines, Pall Corp. , Robert L. Brown
Designing a separation process
Rocger W. Cusack, Koch Process Technologies, Inc.
Separation simulation via spreadsheet
Andrew Wilson, Solvay Specialty Chemical Co.
Processing with supercritical solvents
James McClain, Micell Technologies
Hybrid separation schemes for CO2 removal: Conditioning natural gas
William Echt, UOP LLC
Hybrid separation schemes for producing organic acids
Mathieu Bailly and Daniel Bar, Eurodia Industrie SA
The many faces of ion-exchange resins
James T. McNulty, Rohm and Haas Co.
Demystifying mist eliminator selection
Steven Ziebold, Monsanto Enviro-Chem Systems, Inc.
Put a centrifugal spin on solvent extraction
D. Greg Cybulski and Robert Driscoll, Rousselet-Robatel Centrifugation