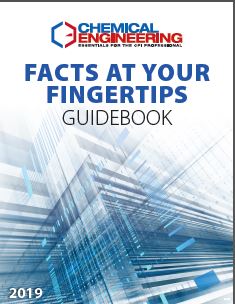
Chemical Engineering’s Facts At Your Fingertips package includes a series of twelve condensed, one-page reference cards that provide useful rules of thumb, common equations and other practical tips for designing, operating and maintaining chemical process equipment.
This guidebook is available in a downloadable PDF.
The topics covered in 2019 include the following:
Selecting a Heat-Transfer Fluid Supplier
Lean workforces are the norm in current plant environments. In the context of heat exchange systems, the current situation amplifies the need to select a heat-transfer fluid supplier with the expertise and technical resources to handle non-routine circumstances. This one-page reference outlines questions that operating companies should consider when selecting a supplier.
Pump Sizing Parameters
A solid grasp of pump sizing allows engineers to make effective economic and practical decisions about process pumps. This one-page reference provides information about two key parameters and other considerations for pump sizing.
Pressure Measurement for Real Gases
The ideal gas law (PV = nRT), relating molar volume of a gas to pressure and temperature, is predicated on two assumptions: 1) that the volume occupied by the gas molecules is negligible compared to the volume of the vessel; and 2) that no intermolecular attractive forces are present. In reality, these assumptions limit the applicability of the ideal gas law, especially at higher pressures and densities, and low temperatures. For accurate calculations of PVT behavior of real gases in industrial settings, engineers have developed many equations of state (EoS) for various conditions. This reference provides information on several key cubic equations of state that attempt to accurately predict real gas behavior.
Fermentation Considerations and Economics
Producing chemicals and fuels by fermentation of renewable feedstocks can offer improved sustainability, lower costs and greater safety compared to conventional thermal processes. But realizing these benefits depends on a careful assessment of the process economics, and an understanding of the differences between fermentation based processes and alternatives. This one page reference offers a brief discussion.
Hygienic Process Equipment Fabrication
In hygienic process operations, proper system construction and fabrication has the greatest influence on end-product quality and the success of process validation. Even well-designed hygienic systems can be compromised by leaching, poor internal finishes and mishandled material sourcing and other fabrication issues. All can lead to contamination and bacterial growth in the system. This one-page reference provides information on key quality-assurance procedures for the fabrication and assembly of hygienic systems that will help prevent contamination and bacteria growth during operation. Contamination can come from unlikely sources, such as process media reacting with rubber over time, causing carbon to be extracted from rubber parts. Pipes can have improper finishes or poor welds, creating safe harbors for bacteria to grow. Following proper procedures can minimize potential issues.
Low-Temperature Handling Considerations
Processes involving extremely low temperatures present unique process design and safety challenges. This one-page reference outlines considerations for low-temperature operations.
Safety Instrumented Systems and Risk
Within the chemical process industries (CPI), the need to design safety systems to prevent process failures from occurring, or to control them when they do, is well recognized, as is the importance of having confidence in the safety systems that are put in place. However, when formalized, the specific terminology, definitions and concepts are sometimes misunderstood, misinterpreted or implemented incorrectly. Provided here is a review of terms and definitions related to determining safety integrity levels (SILs).
Solids Handling: Friction in Bins and Hoppers
To avoid problems with solids flow in bins and hoppers, the friction between the equipment walls and the flowing solids is an important factor to understand. Provided here is a review of flow patterns in bins and hoppers, and practical design considerations for overcoming challenges related to wall friction. In the past, bins and hoppers were typically designed primarily from an architectural or fabrication standpoint (for instance, hopper walls were sloped 30 deg from vertical to reduce the waste of wall materials, or 45 deg to minimize headroom requirements and simplify design calculations). However, experience has shown that designing equipment without regard to the actual bulk materials being handled often leads to flow problems, such as arching, ratholing, erratic flow and even no flow. By measuring the flow properties of a bulk solid, including wall friction, the flow behavior of the material can be predicted, and more reliable hoppers and bins can then be designed.
Industrial Drying: Convection versus Conduction
Adjustment and control of moisture levels in solid materials is a critical aspect in the manufacture of many chemical products. Drying can be defined as the vaporization and removal of water or other liquids from a solution, suspension, or other solid-liquid mixture to form a dry solid. A complicated process involving simultaneous heat and mass transfer, accompanied by physicochemical transformations, industrial drying is often accomplished through one or more of four broad mechanisms, including the following: direct drying (convection); indirect or contact drying (conduction); radiant drying; and dielectric or microwave drying. This one-page reference focuses on the differences between convection and conduction drying.
Surface-Mediated Heterogeneous Catalysis
Heterogeneous catalysis in industrial processes involves a complicated set of physical and chemical phenomena that help lead to products. This one-page reference provides information about the formation of products in an industrial process using solid catalyst materials.
Pneumatic Conveying: Pipeline Bend Challenges
Among the key benefits offered by pneumatically conveying bulk solids is the ability to route materials around obstructions in the plant using bends in the pipeline. However, these changes in direction involve a considerable number of particle impacts on the bend wall as the particles make the turns. This one page reference reviews the potential problems that can arise from particle impacts in pipe bends of dilute-phase pneumatic-conveying systems.
Agglomeration Processes
Agglomeration converts fine powder particles into larger ones by introducing external forces. Major benefits for solids processors include dust reduction, easier handling, more complete utilization of raw materials and densification. Agglomerating particles happens by a variety of means, including mixing with a liquid, applying pressure and heating. This reference reviews equipment for these approaches.